Precasters sound off on how their product can fit nearly any and all needs in commercial construction, especially as the industry continues to innovate. By Taylor Larsen
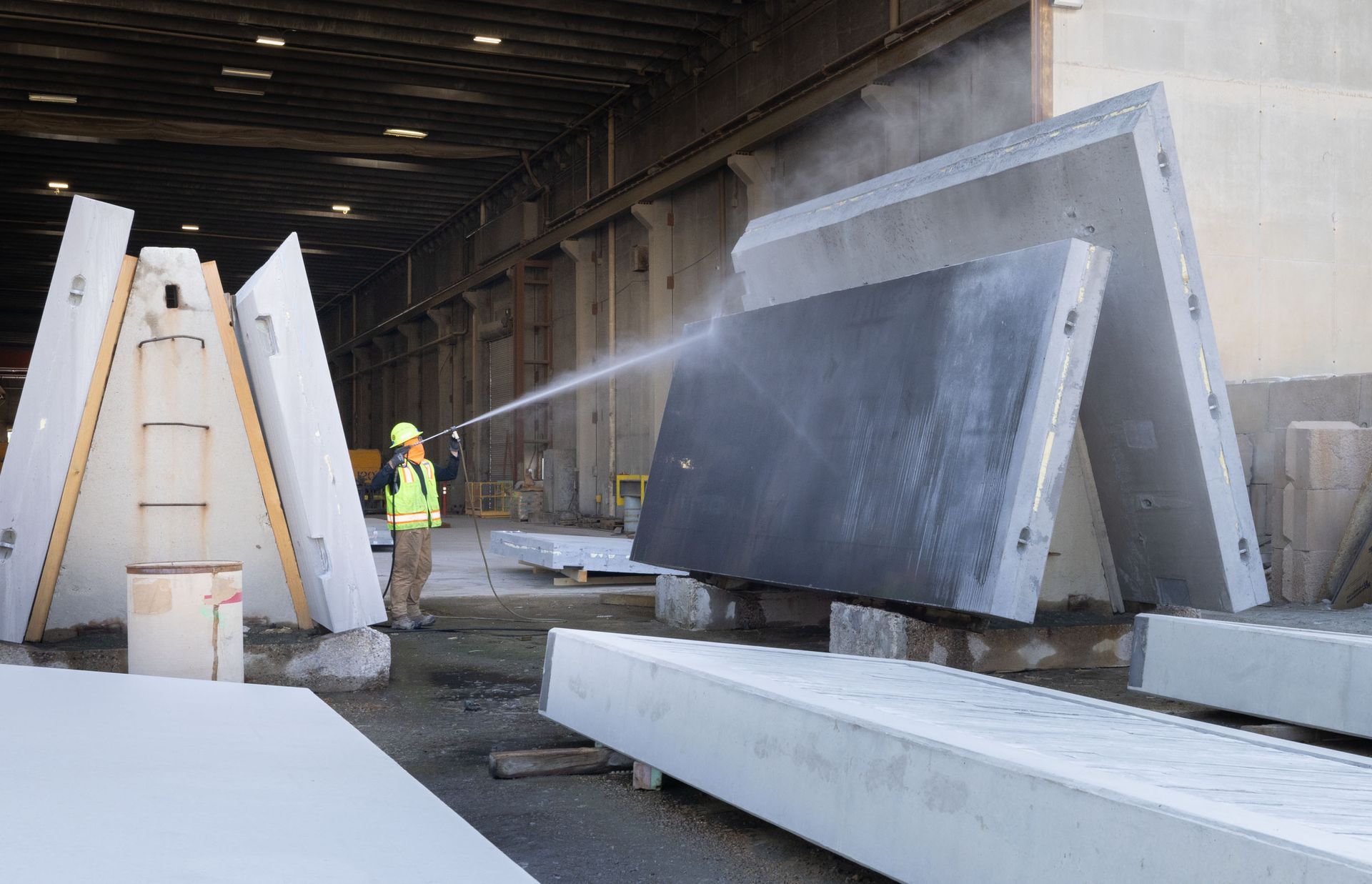
Markets and Verticals
From a regional perspective, Jim Schneider, Executive Director for the Precast Concrete Institute Mountain States, said there are plenty of possibilities for the industry amidst federal legislation and funding over the last few years.
“As roads, bridges, and other vital infrastructure are replaced,” he said, “the precast industry is ready to support infrastructure initiatives wherever they are needed.”
Parking structures and infrastructure will continue, but other markets and verticals are available like schools and the influx of data center work taking over the west.
The clear consensus among precasters is product and market diversity win the day. It’s how they can supply Utah County with the right product to build up neighborhoods, send box culverts down to Southern Utah to mitigate flash flooding on roads, and deliver bridge girders and MSE walls in Davis County to keep transit moving.
While there are plenty of competitors in the market, the array of products to perfectly meet owner needs will only grow in importance, especially as communities fill out in the coming decade.
David Wallers, Division Manager for Harper Precast, said that Utah will continue to embrace precast, especially at the larger firms and owners like Pacific Power, UDOT, and large-scale developers chief among them.
“Precast has such a huge advantage on public safety,” Wallers said. Its use will only continue to grow, especially as his team pours 200 yards a day. Highway projects from UDOT, like the current and future phases of Bangerter Highway, are a case in point, especially as precast evolves and improves with changes in materials.
For Wallers and the Harper Precast team, box culverts, MSE walls, electrical vaults, sound walls, and plenty more—the list of products to meet owner needs is extensive, and precast has the power to meet what emerges in the future.
One interesting product is the ballistic panel market, something that has been a key differentiator that reinforces Waller's point about product diversity and the ability to be involved in multiple markets. Harper Precast’s specialized product is UL 10 752-rated precast walls manufactured in their North Salt Lake facility, which are approved to withstand a .50 cal bullet from 40 feet away.
Changing Materials; New Techniques
Wegner said that concrete has evolved substantially over the last 10 years. The standard precast mix for bridges has gone from a 28-day break strength of 6000 PSI to between 8,000-10,000.
“It allows us to do a lot more,” he said. “We can stretch bridge spans on super long girder from 160 ft. to 205 ft.”
New, efficient girder shapes, new techniques like pre-stressing, and other innovations have helped the industry meet its most pressing needs through precast concrete.
Within the concrete evolution, Wallers noted the switch from fly ash to pozzolan in their concrete mix.
While a receding fly ash supply was one reason, the Harper Precast team has found that switching has reduced “concrete cancer” from alkali-silica reaction while keeping set times moving. Air entrainment is more stable while their concrete has become denser and less permeable. All of it goes to making a cost-effective switch that has helped their team stay competitive.
Schneider at PCI Mountain States noted that fly ash has long been a reliable option as a supplementary cementitious material but, as a byproduct of coal, “fly ash becomes a less reliable solution as time goes on.” Like the use of pozzolan, he said, there are exciting innovations within the larger concrete industry to reduce or replace cement with other materials.
“The National Renewable Energy Lab is working on a project to explore the use of mine tailings as replacement for cement, and there's a fascinating study at Colorado University - Boulder that's working with microalgae to decarbonize concrete,” he said. “Lots of exciting possibilities are on the horizon.”
Solutions are out there to gain additional efficiencies but lose out on the most important variable—price. Whether it is rebar reinforcing alternates instead of scrap steel, or the use of cement alternatives, an industry driven by money and schedule is loathe to adopt something where a cheaper alternative gets the job done well.
It’s a microcosm of their work to meet owner needs.
Even with schedule benefits and cost assurances, many companies have always worked with cast-in-place as their casting method continues to do so. Especially with many of the major commercial builders self-performing, Wegner noted: “Why would they do something else?”
He said that it is incumbent on the precast industry to win owners’ trust and match those promises with what is delivered to the job site.
Whether architectural precast walls (left) or box culvert (right), precast’s standardization of manufacturing, QA/QC, and delivery make it the go-to on infrastructure projects as everything can be built off-site before arriving for placement on the job site. (photos courtesy Harper Precast)
Emerging from Labor Struggles
As for the workforce, it’s a pain point—for some more than others.
Martin said that certain labor issues for their team are looking to be solved by technological advancements in the precast manufacturing space in the form of a new facility to further automate the precast process. Geneva Pipe & Precast’s parent company, Northwest Pipe, pledged $18 million in capital improvement projects for their Utah offices in 2021, helping the Salt Lake branch to construct and supply a new facility, with state-of-the-art precast machinery from Europe. Geneva Pipe is hosting an open house for its latest reinforced concrete pipe precast facility in early October.
While the company has extended the design life of its two Utah manufacturing facilities to 50 years with machinery repairs and renovations, the investment goes back to labor. Martin said the manpower required to operate the new equipment will be just four precast manufacturing pros, instead of the 12 currently required at their Salt Lake plant, along with two others helping to keep the digital aspects of the technology running at an efficient rate.
Growing through Efficiency
Wegner said the industry has made major inroads on longevity, where once a bridge would need to be replaced after 30 - 40 years, bridge lifespans are extending 75 or more years. That, combined with precast’s centralization of materials and production gives it an efficiency bonus that may win over an owner looking for concrete solutions in their next project.
This extension of a project’s life cycle has been a big win in the wastewater field. Martin said his team has utilized fiber-reinforced rehab panels to extend the life of wastewater infrastructure. The corrosion-resistant panels can be easily applied to the interior walls of new and existing precast structures and provide a long-term solution in the fight against hydrogen sulfide gases that give the wastewater industry fits.
"Perfect pipe" has been one innovation that has picked up steam, too. The sewer industry had been on the lookout for a new solution for years to combat sulfuric acid and Geneva Pipe looked to deliver in the form of high-density polyethylene-lined pipes and manhole covers to keep sewage’s corrosive effects separate from the concrete. The 50-year design life is a major change from the 5-10-year design life of unlined products. The premium nature may cost owners a little more, but the shift to longer design life, with less maintenance, continues to pick up pace.
Upward Trajectory
All of those interviewed said that business is good, and the power is in their hands to meet market demands and make business even better. With growing product lists and growing capabilities, precast is trending up; its market share expanding and solidifying as it goes.
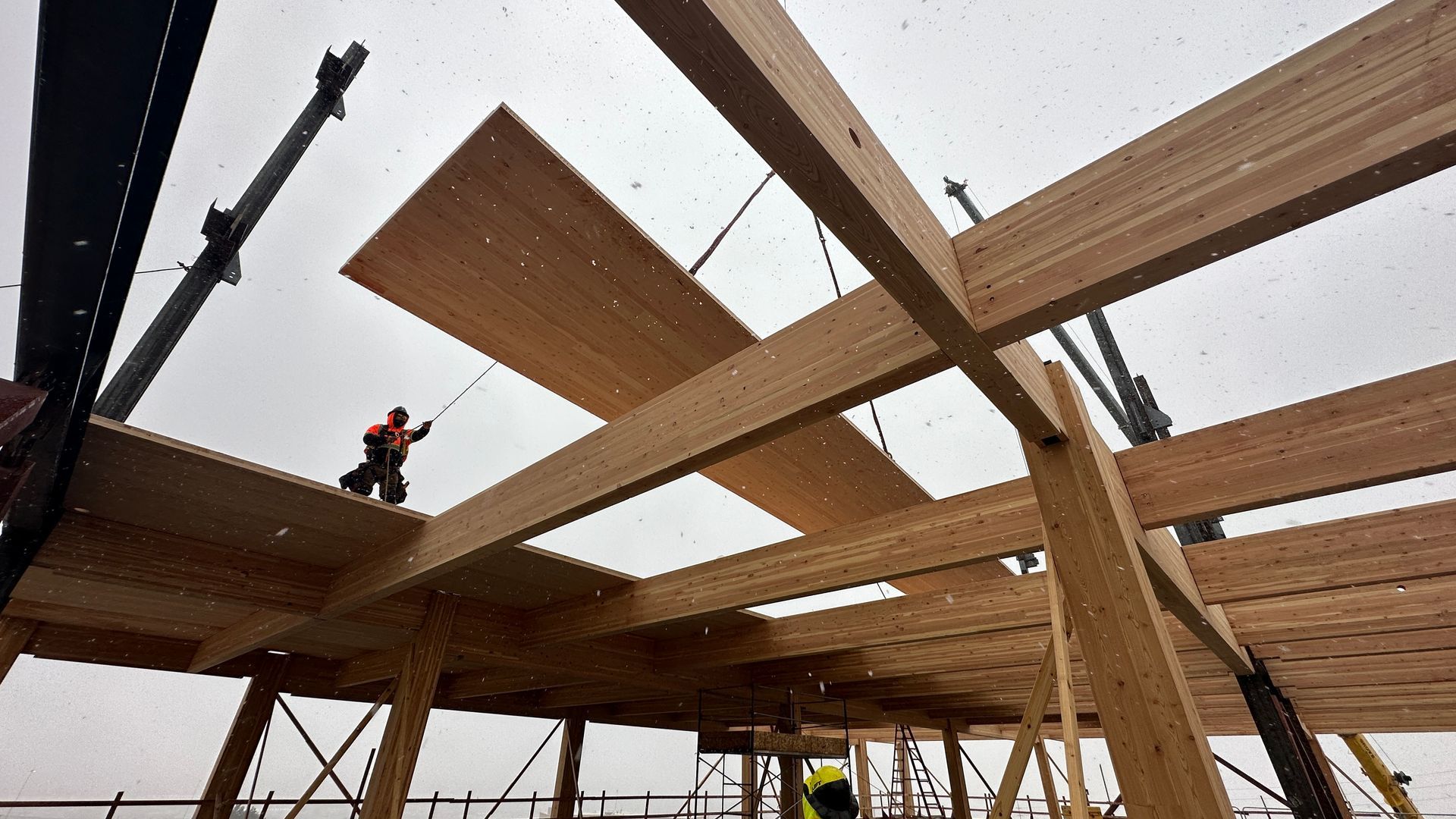
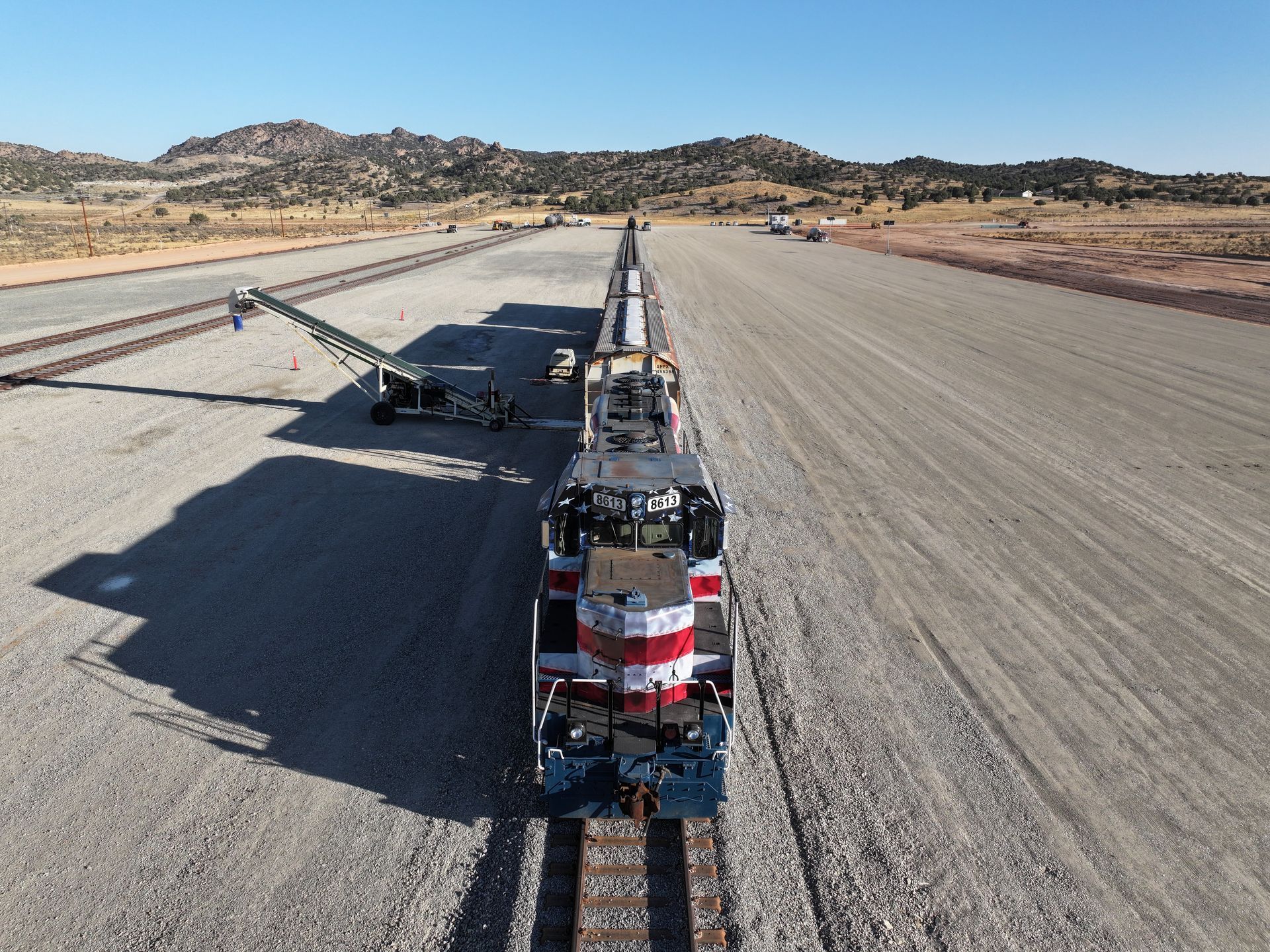
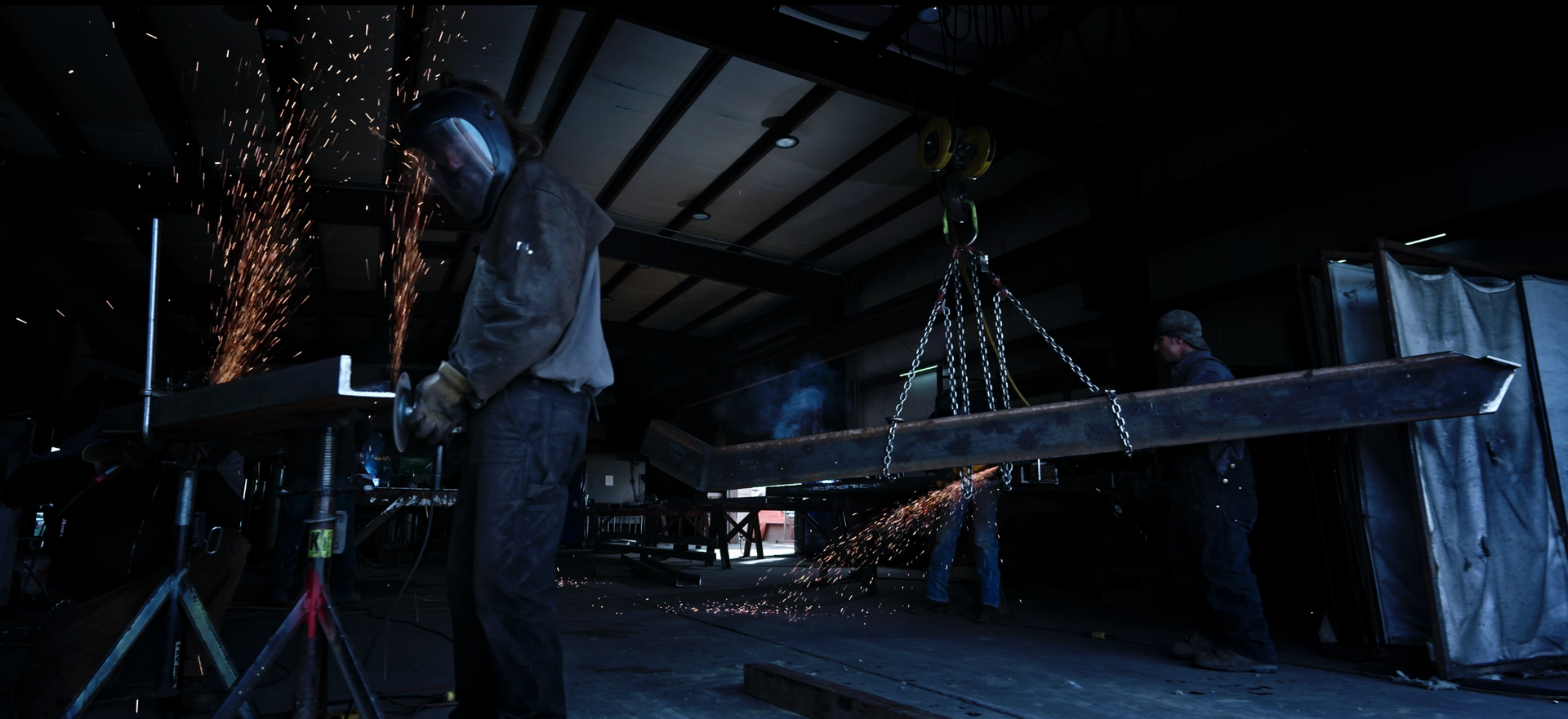
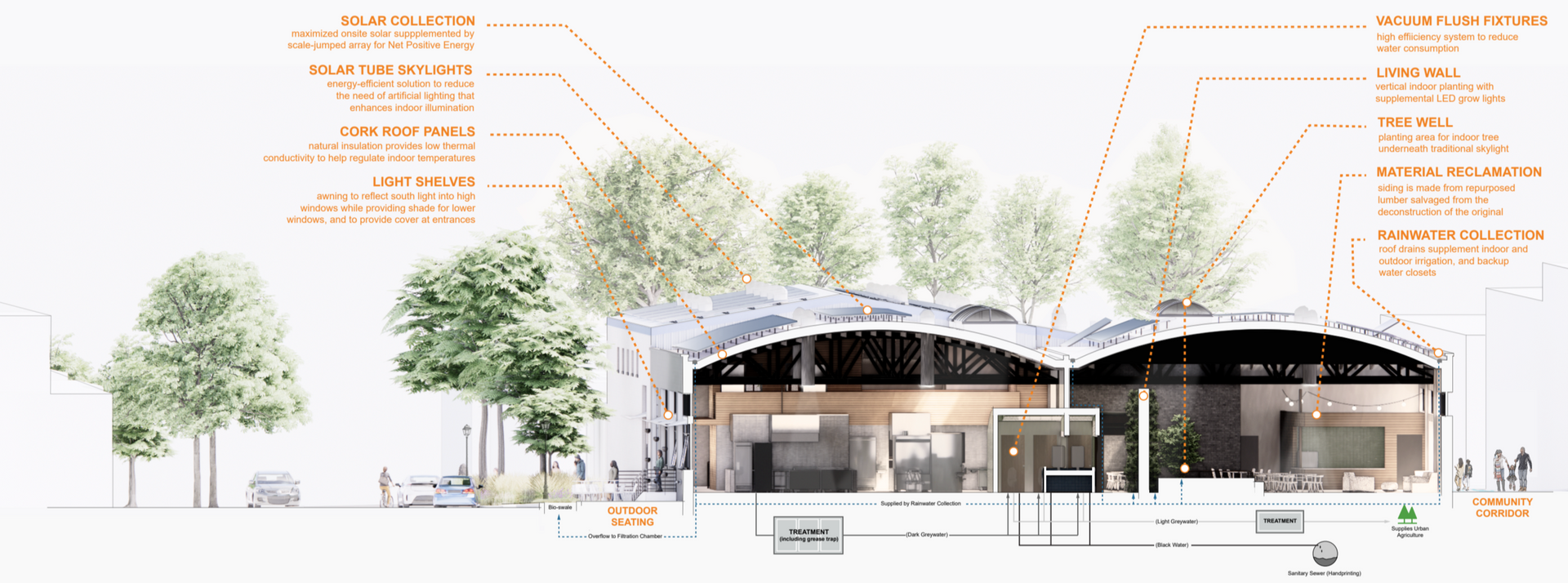
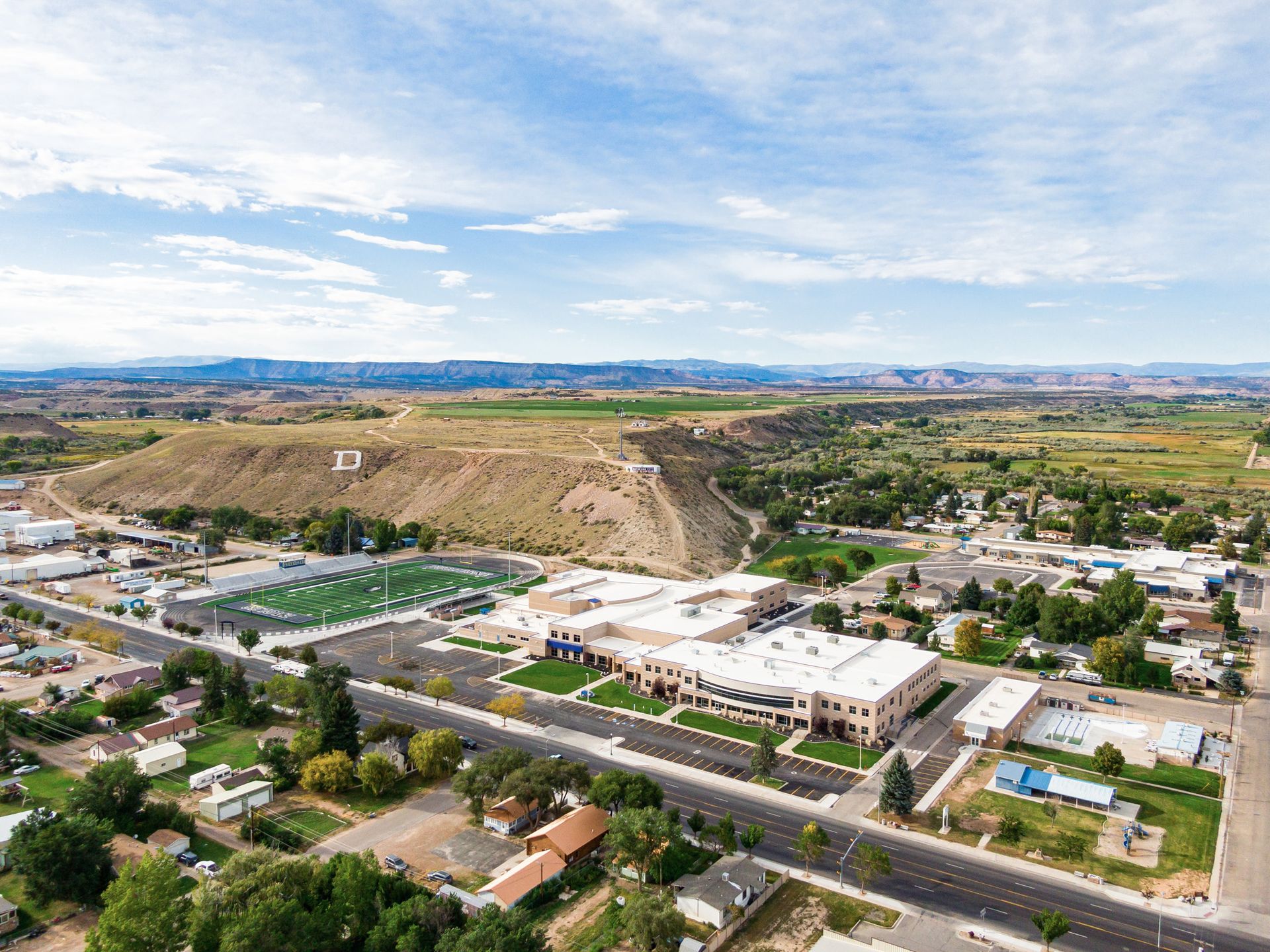
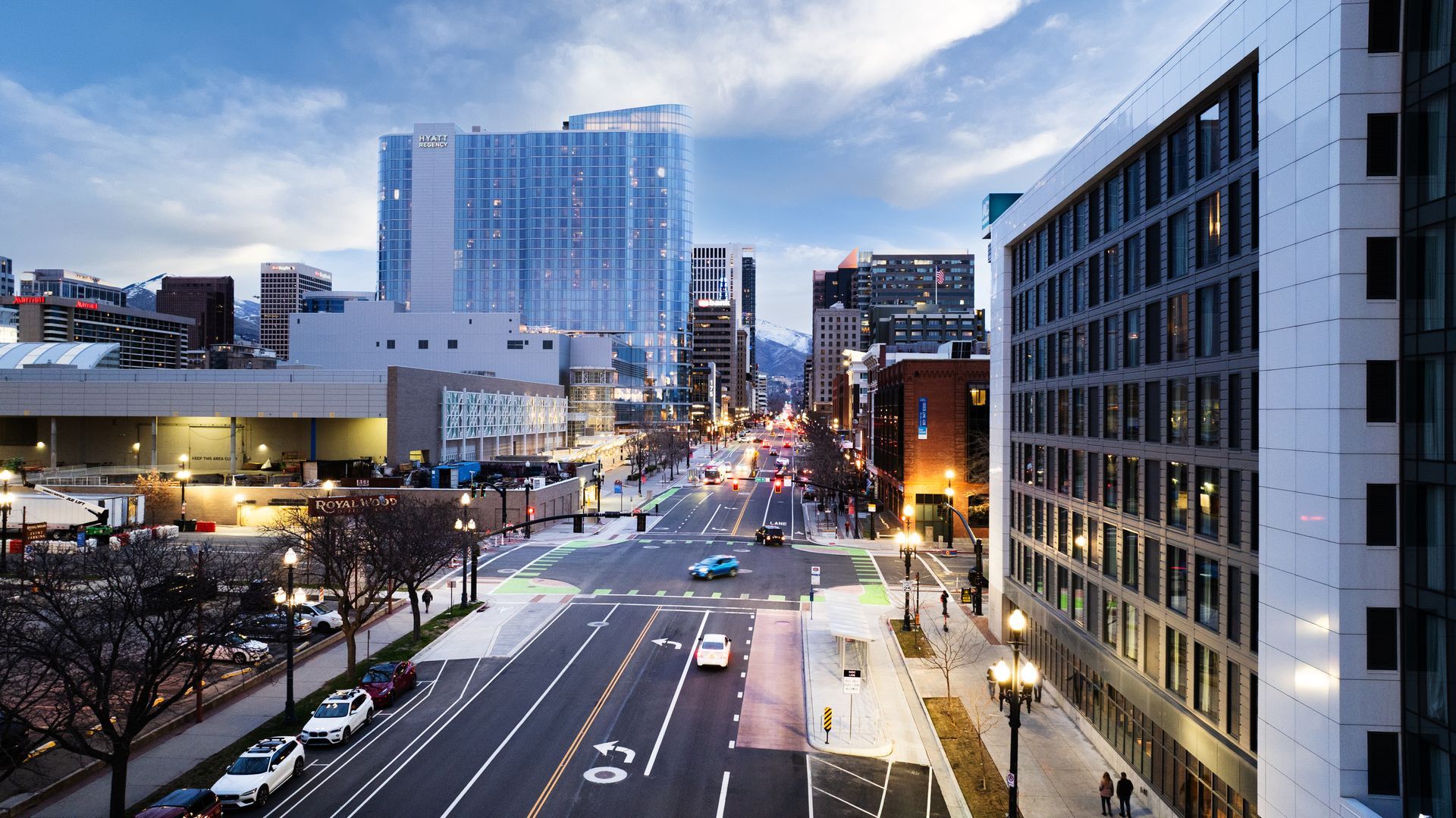
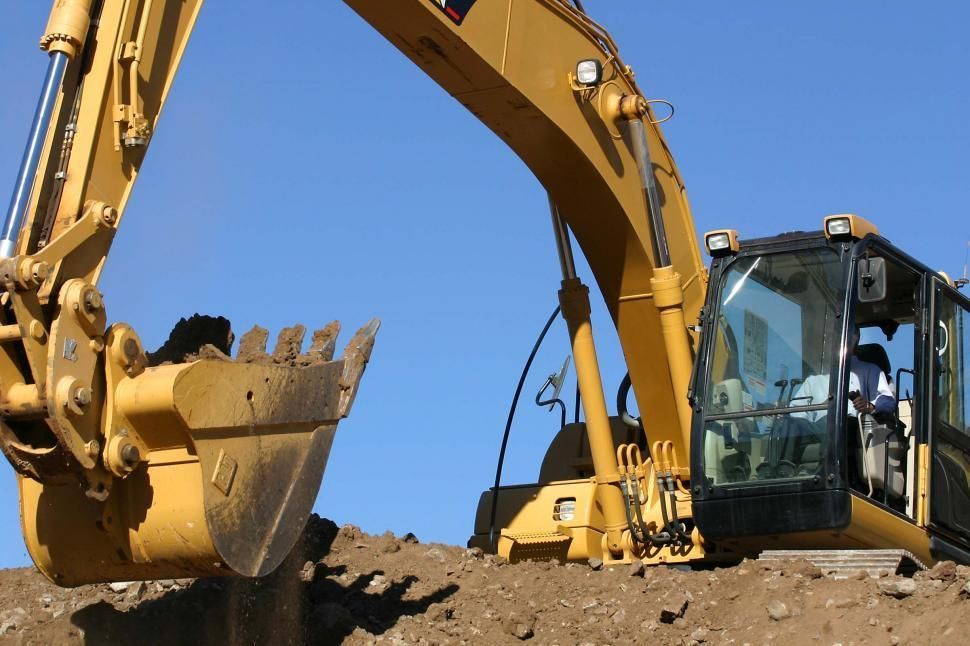
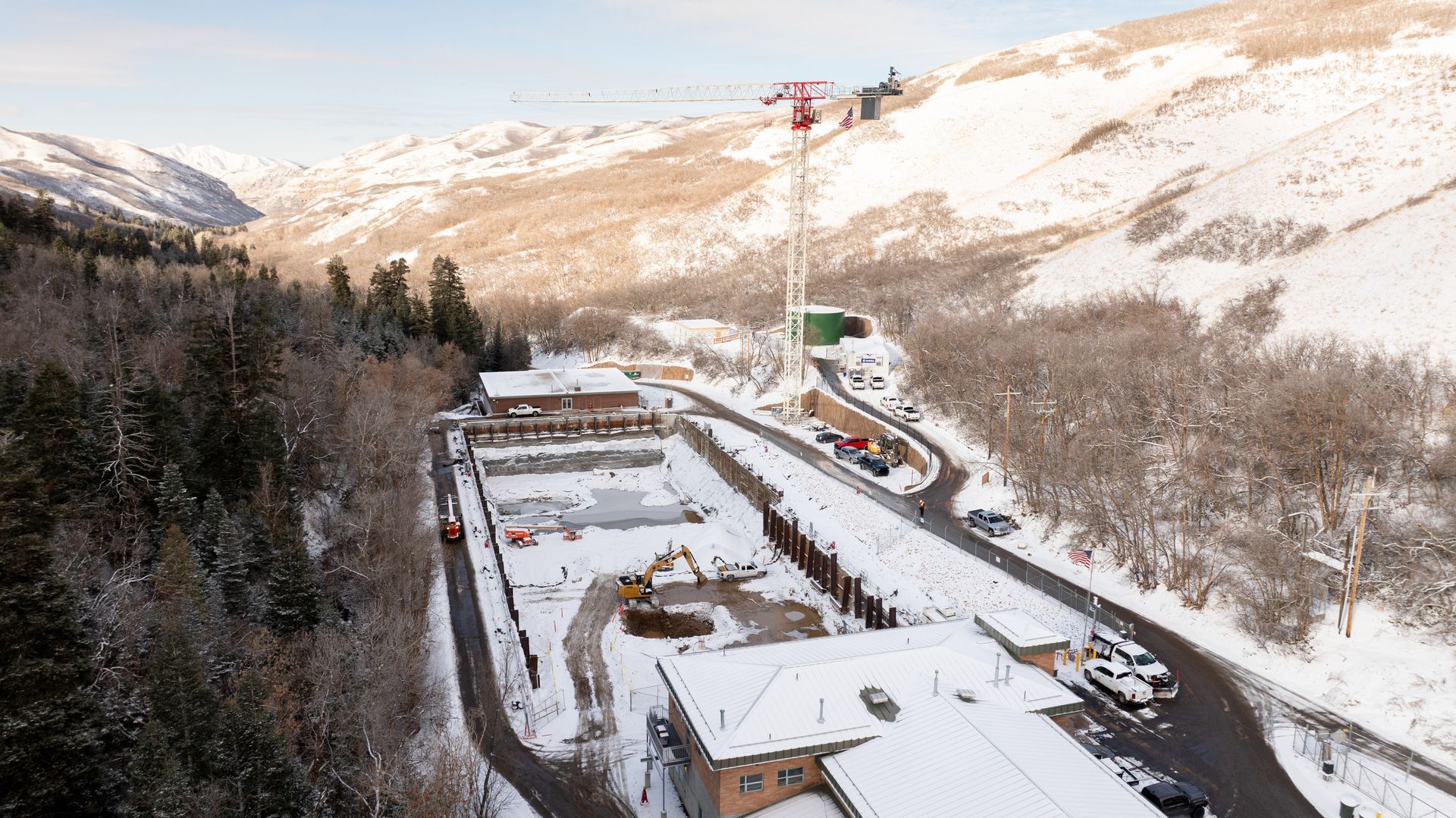