Glazing continues to catch the eye in today’s built environment. Industry leaders say that improvements are being made at all levels of their field, even as bringing on new employees remains a persistent challenge.
Model Association
This issue is significant enough to take UGA beyond Utah’s borders—as evident by the National Glass Association inviting the three mentors of the UGA apprenticeship program to speak about retention, training, and association-building at GlassBuild America’s glazing executives forum.
“It was exciting to get up there and talk to everyone about what should be done for these guys to be more important, not just for the company but the people [and] give them a legitimate trade,” said Hall.
The forum provided a place for the mentors to show their passion and showcase the power of an effective glazing association. Said Lynch, UGA Mentor as well as Lead Installer for Midwest D-Vision Solutions, “I’m thankful we did because I didn’t realize the need” beyond Utah.
In the Beehive State itself, Reynolds said UGA has brought everyone in the glazing industry together to advocate for their trade. He said that the unity and trust is at such a level that certain companies have utilized team members from other companies to not just complete projects, but to retain their glaziers by ensuring they always have work.
Lynch agreed, saying, “We are working hand in hand with these other glass companies […] and creating this neutral ground where we come together with a common need—employees.”
Technological and Other Advances Help at All Levels
Labor remains the biggest constraint, but those interviewed said much has been done in the last few years to bring in labor-saving tools, allowing more people to enter the trade as well as remain longer.
Reynolds mentioned how pre-fabrication and pre-installation has been instrumental for his company to meet the building schedules on dozens of projects.
“We’re trying to do as much as we can here in the shop before we head out,” he said. The controlled environment has allowed for pre-fabrication, pre-installation, and even pre-glazing of certain products to make for quick work out in the field.
The top-down approach to allocate capital has been a success—with 25% more people working on fabrication contributing to double, and even quadruple, the production levels of the Midwest D-Vision Solutions’ glazing work. CNC machines have provided savings in not just project precision, but in employee labor where it can be best utilized. It keeps people more engaged at work and engaged in safer practices.
But the bottom-up approach is working, too. “We’ve been asking our staff ‘Tell me what you need to be more efficient,’” said Reynolds. Those discussions led to the purchase of a second CNC machine after employees made the pitch to create a better work environment.
Reynolds said their work on interior glass has seen plenty of innovation. Ambient-controlled glass and electronically-controlled glass, for instance, function much like transition-lensed glasses. With innovations like these, interior glass can switch from transparent to opaque to add a privacy layer while still benefiting from daylighting.
Some innovations feel a bit futuristic, but they’re changing the business landscape—like the embedded LED lights in places like the Security National building in Murray. Companies utilizing these emerging technologies, Reynold said, are trying to take the branding and signage budget and put it into the glass budget for a higher-end finish and look.
Losee said that energy codes are becoming more stringent, but the industry is answering with better technology and better products, especially the advancement of softcoat low-emissive glass, higher-reflectivity glass for solar performance and privacy, fritted glass for bird safety, among other products.
Glazing Trends to Watch
On top of employment, retention, and innovation, there are price escalations, higher interest rates, rising wages, and the ongoing supply chain struggles combining to leave the future of glazing and the overall built environment a bit murky, according to those interviewed.
The supply chain remains unpredictable in lead times and pricing, but both are improving.
Lead times are finally coming down from pandemic levels and far better than the 20-week lead times that required sequencing miracles to finish projects a few years ago.
Price increases from the beginning of 2020 to now range from 40% more on floated glass products to 25% more on aluminum from pre-pandemic prices. While prices are decreasing at a snail’s pace, interviewees said the stability in pricing is a welcome change from years prior.
Losee explained that budgets developed two years ago, however, are struggling today in funding the entirety of the project.
In its place, “these beautiful concepts are being designed down,” he said. But there’s a reality to how far those measures can go. “Stuff costs what it costs. You can’t get the exact same for less money. […] Quality will be affected somewhere.”
Will glass continue to make inroads and be a preferred building solution inside and out? With recently-completed, award-winning projects like 95 State, Ivanti Headquarters, and Zions Bancorporation Technology Center showcasing why both interior and exterior glazing are here to stay, glazing experts are confident that their field—from labor to emerging technology—has the right answers for the built environment.
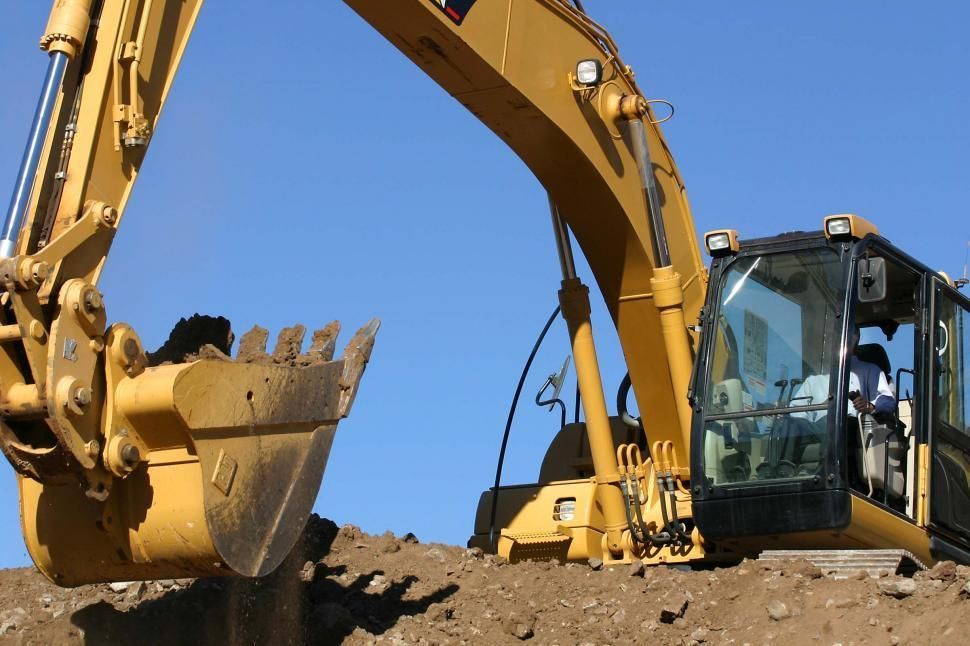
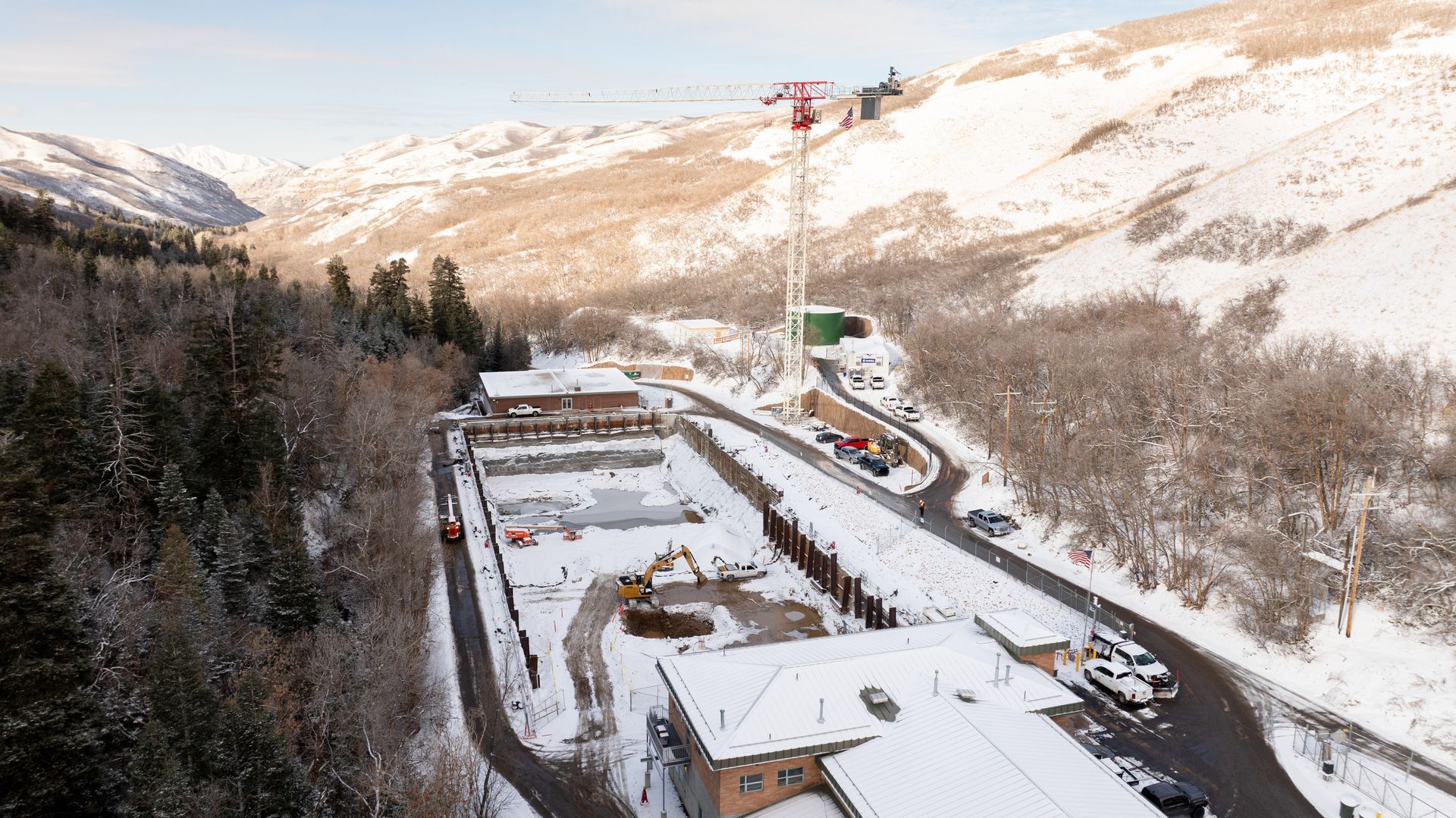
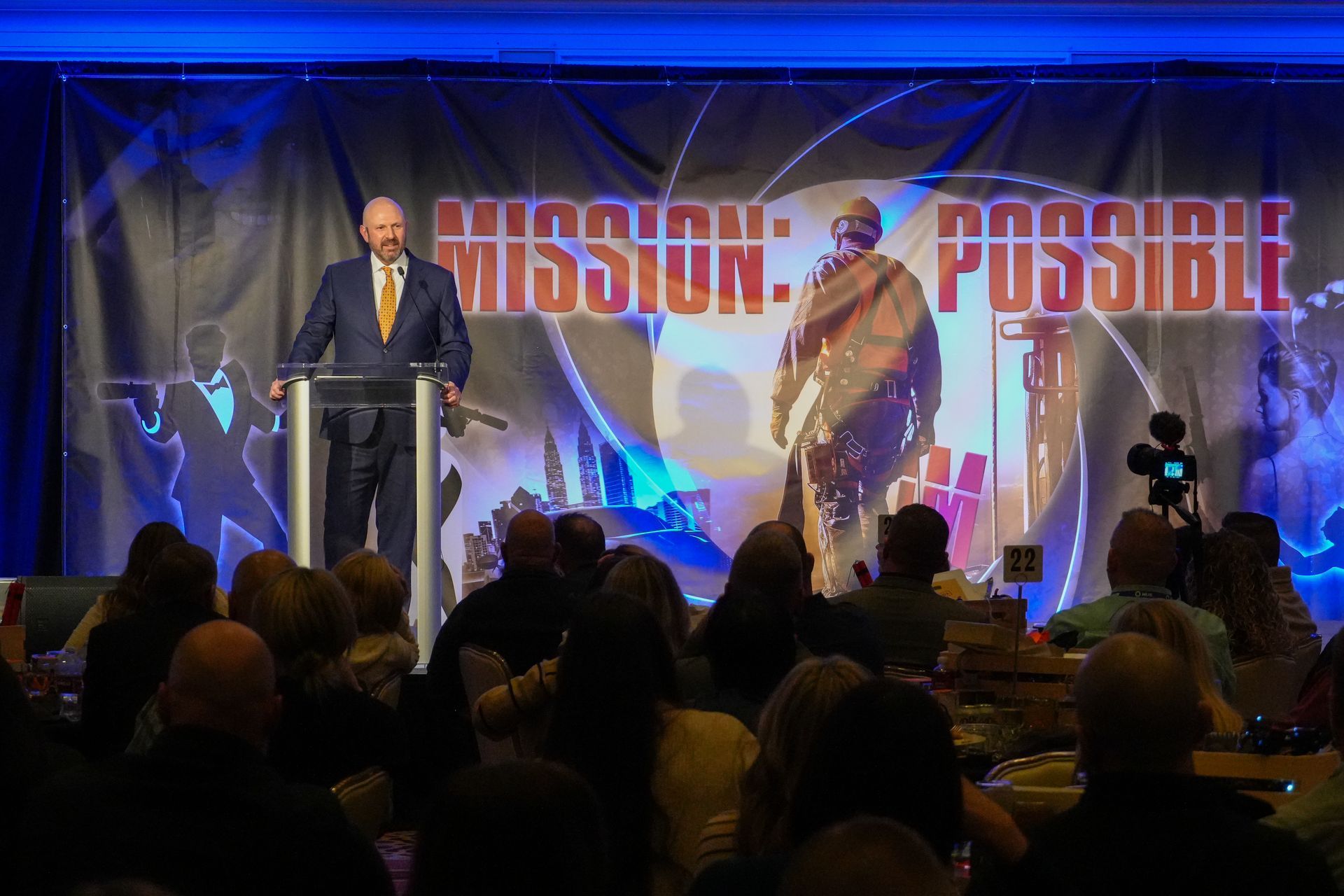
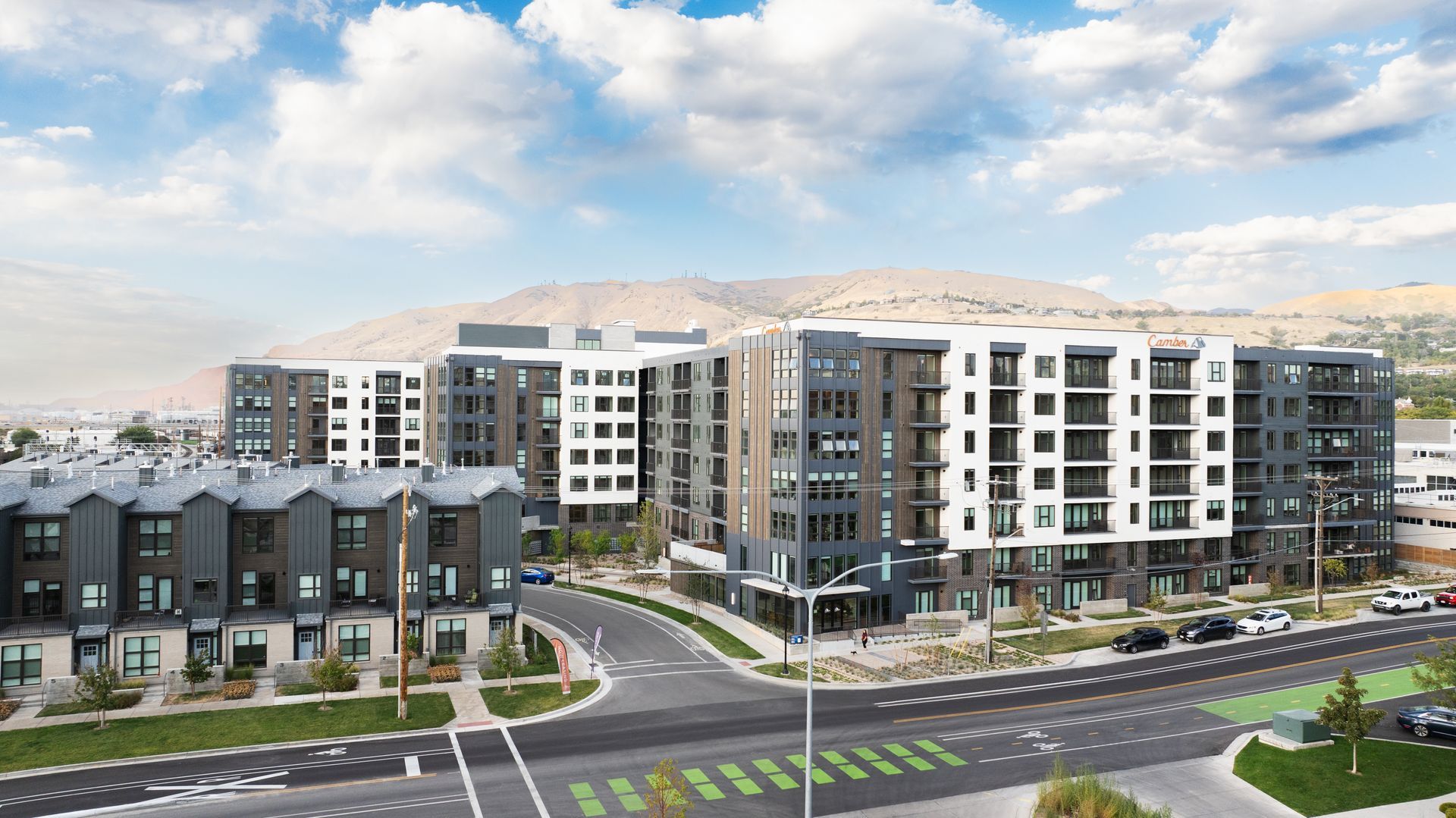
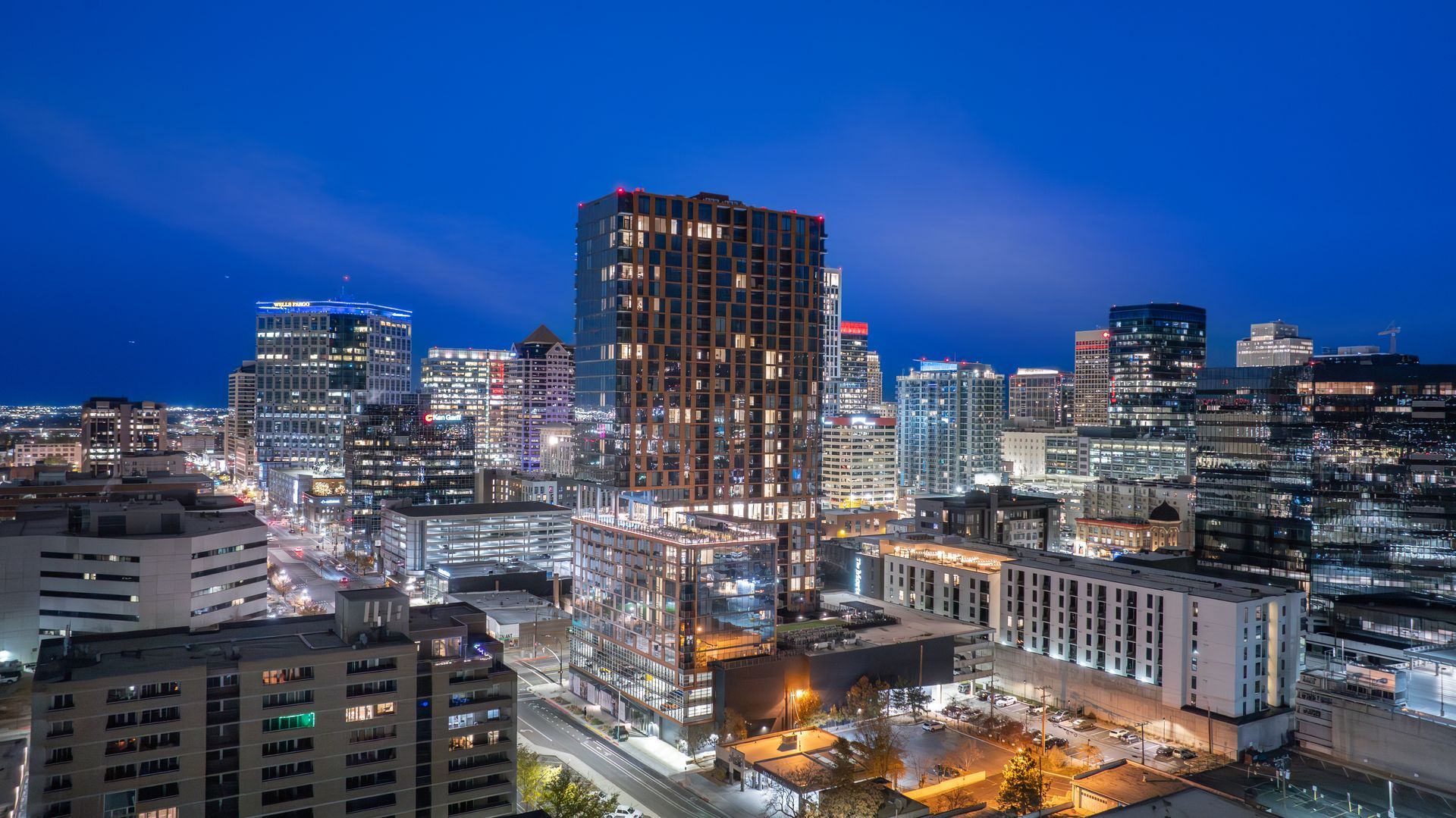
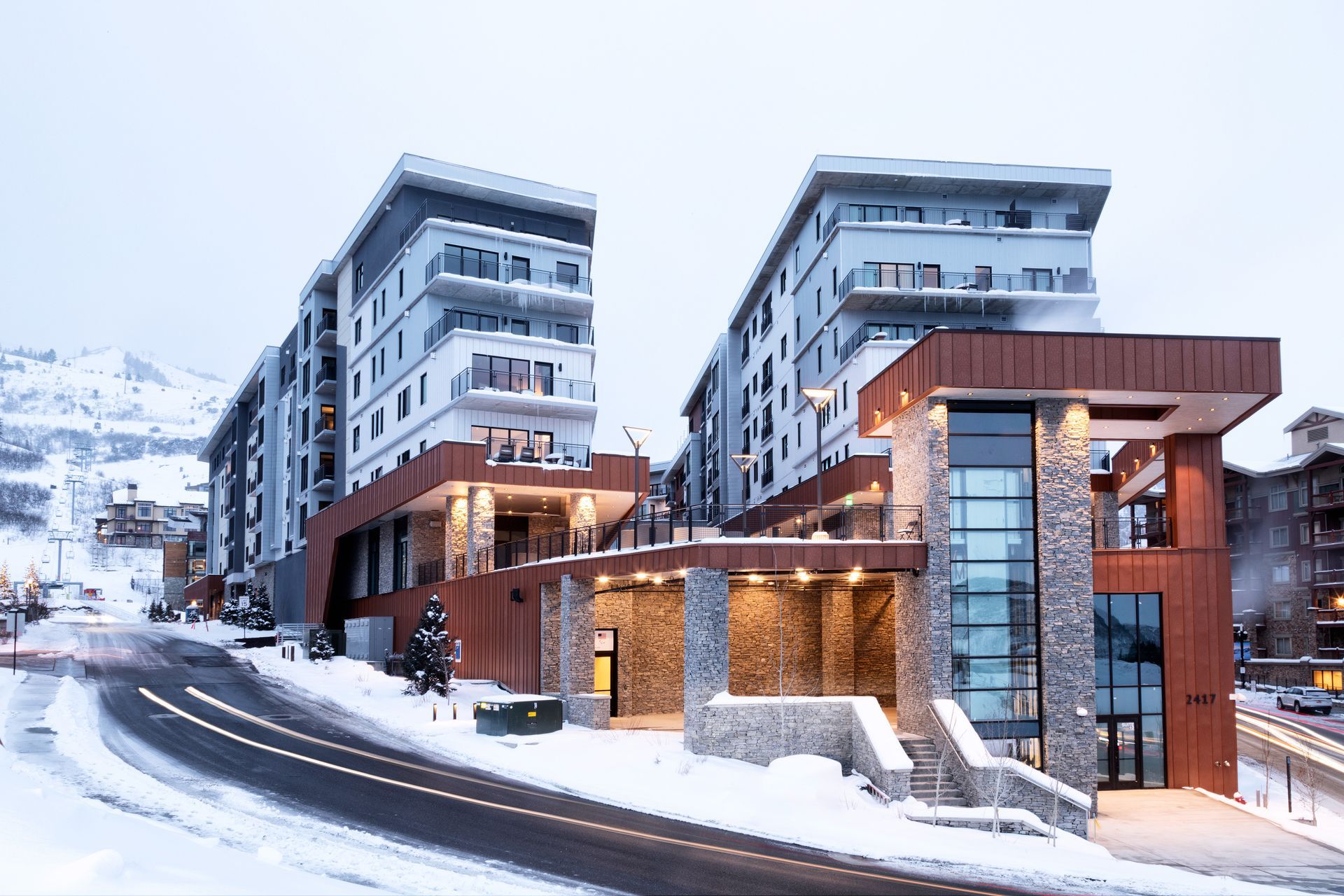
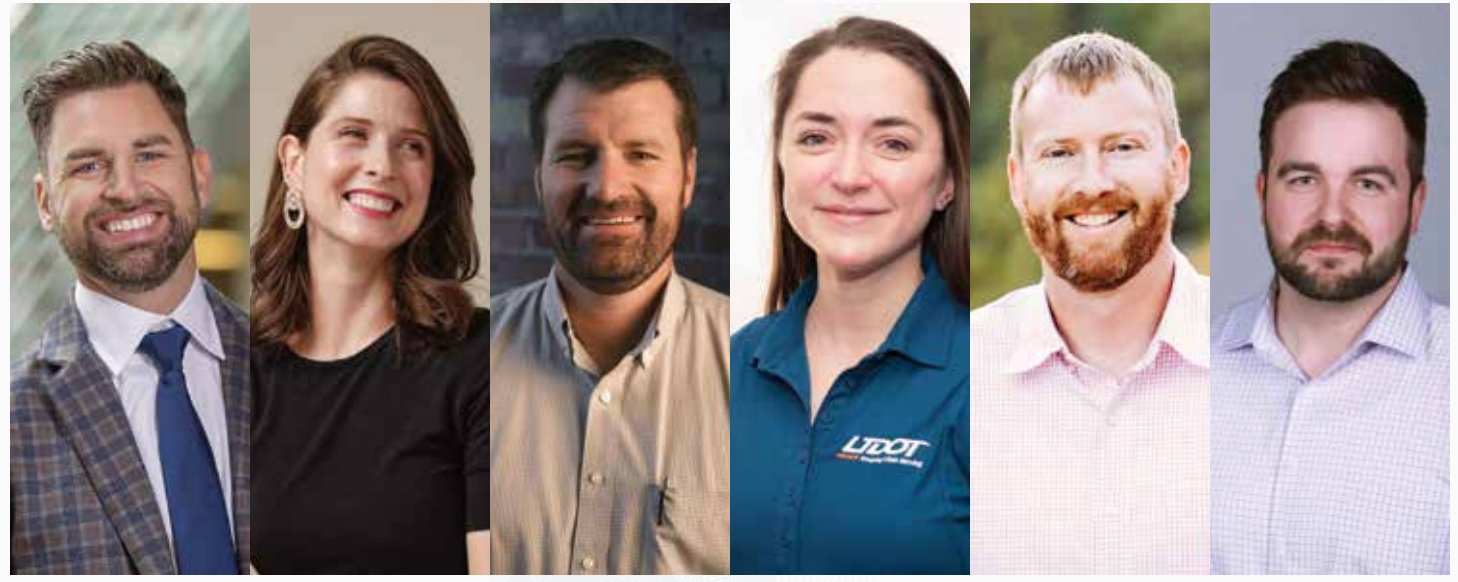
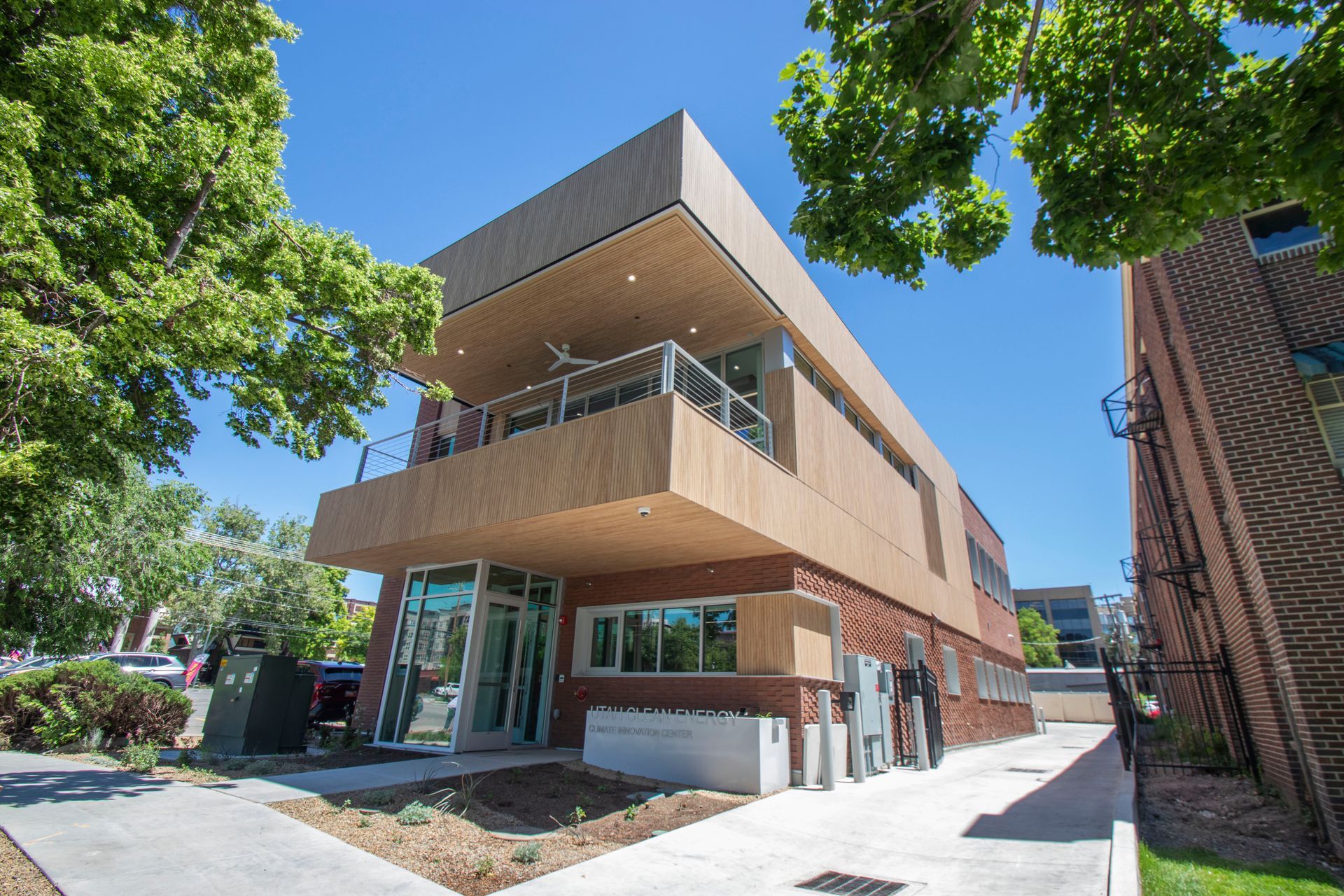